Switching From Hydraulic to Electric Actuators? Follow These 3 Easy Steps
By John Fenske on March 6, 2025
Hydraulic actuators are deeply entrenched as a workhorse automation technology, but advancements in electric cylinders have made electric actuators better suited for certain jobs. In industries ranging from timber to packaging to medical devices, engineers are finding compelling reasons to make the switch from hydraulic to electric actuators.
Although hydraulic cylinders are rugged and produce extremely high forces, their electric counterparts offer greater motion control flexibility, require less components and present minimal environmental and safety risks. Thanks to their better process control, electric actuators go a long way toward enhancing product quality, reducing scrap, increasing throughput and improving overall profitability.
Switching from hydraulic to electric actuators may feel like falling into an unfamiliar world, but following these simple steps will ensure you land on solid ground.
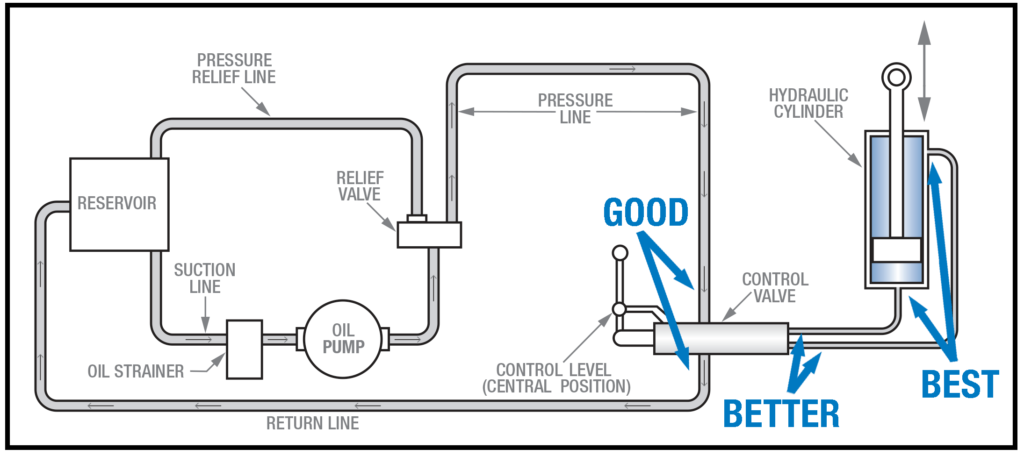
Step 1: Determine the Actual Forces When Sizing Your Cylinder
Specify your electric actuator based on your system’s required forces. However, simply multiplying pressure and area assumes the maximum-rated pressure of the hydraulic system. This can lead to an oversized electric cylinder. Avoid oversizing by measuring the hydraulic pressure during operation.
To obtain the most accurate pressure reading, measure as close as possible to the point of work — i.e., the hydraulic cylinder (Figure 1). Accessibility may make it a challenge to obtain an exact pressure reading, but even an estimation within 15 percent of the actual force will be effective.
Typically, there are three measurement locations:
- At the valve. Because this location is furthest from the point of work, it may cause errors in actual versus measured pressure values.
- Between the valve and cylinder. A better option is to measure pressure between the valve and cylinder. Keep in mind that needle valves and other inline accessories may influence the pressure value.
- At the cylinder. Measure pressure at the cylinder itself for the most accurate pressure reading. However, it may be a challenge to access this location.
Best practice is to measure pressure on the cylinder’s extend and retract ports. Some hydraulic systems have a high return pressure between the cylinder and the valve, which can impact output force, so it’s also best to measure both the system’s return pressure and working pressure.
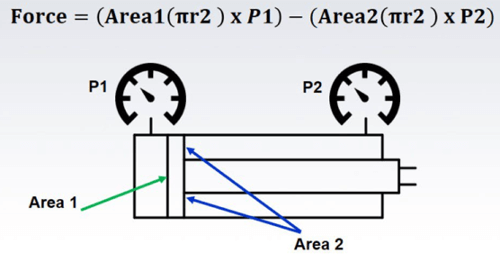
Step 2: Define Your Motion Profile
The next step is to understand your motion profiles, cycle rates and throughput. Determine which is more important:
- Moving at a given rate (cycle time).
- Moving a distance in a given time (velocity).
Your choice will impact your motion profile and inform you on how to size your actuators and drives. High cycle rates involve faster movements and require actuators that accelerate and decelerate quickly. Keep in mind, higher cycle rates increase heat generation and mechanical wear. To help you optimize your motion profile and minimize wear, companies like Tolomatic offer sizing tools to help you select the best components for your application. Tolomatic’s tool even automatically flags components that exceed their thermal limits.
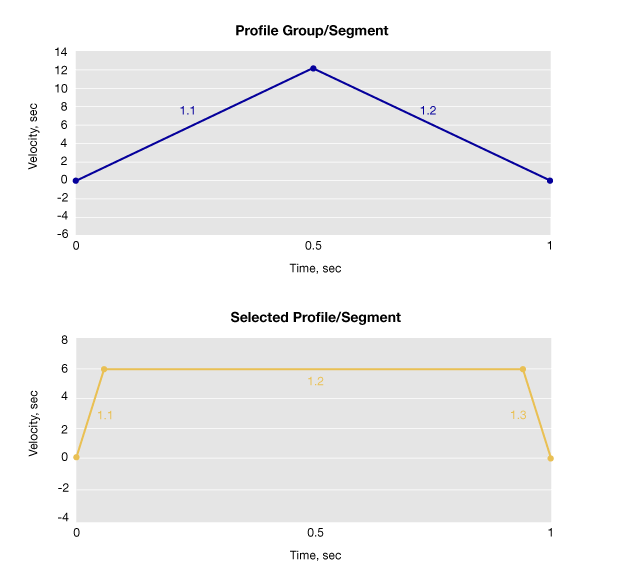
Step 3: Use a Reputable Sizing Software
Good actuator sizing software is an indispensable tool for transitioning from hydraulic to electric actuators. For example, Tolomatic’s software automatically calculates and determines which actuators will work best given your speed, force and life requirements. To begin, simply define critical parameters like motor mounting, actuator orientation, stroke length and environmental conditions. Next, define the loads and velocities for the stroke segments you specify; the number of segments and their characteristics are up to you. Finally, the tool displays Tolomatic products that fit your parameters and motion profile.
Interested in making the jump to electric? Learn more in our white paper.