Roller screws for high force linear actuators. What type’s best?
By Tolomatic on March 7, 2017
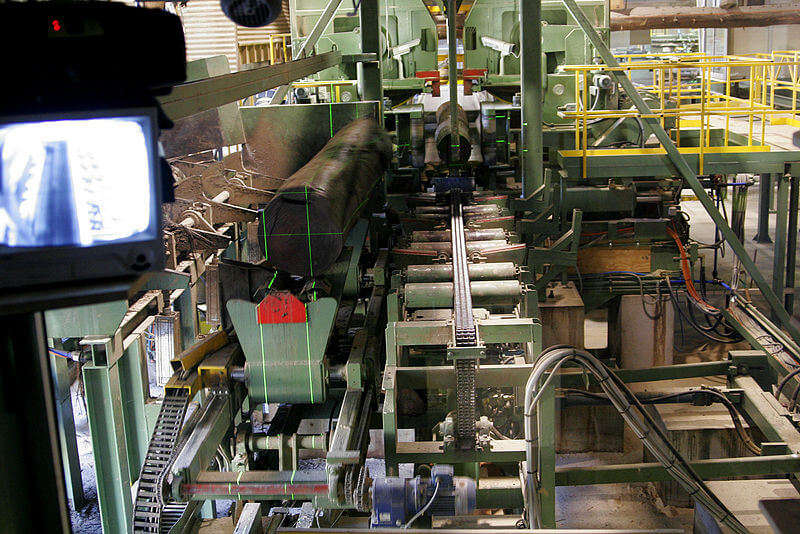
Standard roller screw? Inverted? Now that electric linear actuators are being adopted for high force applications, there’s a debate about what type of roller screw is best. Roller screw actuators can deliver forces of over 50,000 lbf (225.5kN), but there are different screw types out there.
Selecting the best screw type for a high force linear actuator can seem a daunting task, but it doesn’t have to be. Start with our Guide on the three common screw types for electric actuators, their advantages and disadvantages.
Then go deeper with this review of screw selection for high force linear actuators.
Roller screw benefits
A roller screw has triangular-shaped threads that mate with threaded rollers in the nut creating an extended contact zone. The extended contact zone results in very high force transmission capabilities and dynamic load rating (life) in a more compact package than traditional ball screws.
The use of these screws allows engineers to specify electric linear actuators in applications once dominated by hydraulic cylinders. Compared to a fluid-powered cylinder, an electric linear actuator powered by a roller screw is low-to-no maintenance, longer-lasting, capable of higher speeds and much more accurate. This kind of electric high force actuator offers the advantages of programmability, fast changeovers, easy data collection and leak-free operation.
Standard roller screws
Usually, in a standard roller screw, the threads on the shaft and rollers are case hardened and then precision-ground. This yields a deeply-hardened surface and precisely matched components that maximize the force transmission capabilities of the screw and provide the highest Dynamic Load Rating (DLR). These screws last longer, making them a better choice when it comes to long-term value. There are other methods, such as rolling and whirling, for creating the threads in roller screws, but the precision of the thread form is not as high. This lessens the overall force transmission capabilities and Dynamic Load Rating (service life).
A standard roller screw that’s integrated into an actuator is easily re-lubricated from the actuator rod or an access port in the side of the actuator. Easy re-lubrication can mean longer screw and actuator life.
Inverted roller screws
In an inverted roller screw, the functions of the nut and screw are reversed — the rollers move inside the nut. While the inverted design can save space, it creates some challenges with manufacturing the threads on an internal dimension (ID) of a tube. While it is possible to precision grind the threads on the ID of the tube, it is much more expensive due to the longer grinding time required as compared to standard roller screws. It is also possible to whirl and roll the thread forms on the ID of the tube, but these manufacturing methods are not as precise and will lower the overall force transmission capabilities and service life of the resultant product.
An inverted screw that’s integrated into an actuator is more difficult to access for re-lubrication. Applying grease often requires disassembly of the actuator.
DLR (Dynamic Load Rating) explained
DLR is a bearing term that’s also used with electric linear actuators that have roller or ball screws. Dynamic Load Rating is a theoretical, statistically-based value of the constant load that a ball bearing or power screw can carry for 1,000,000 revolutions with 90% reliability. The DLR of a product is usually provided by the manufacturer. The comparison in the table shows a standard, precision-ground roller screw actuator from Tolomatic compared with a competitive inverted roller screw actuator.
Get everything you need
Screw selection is a critical factor when specifying electric high force linear actuators. The two roller screw types, standard and inverted, differ in terms of DLR and service life. Standard design screws, with their precision-ground threads, provide maximum force transmission and life.
Tolomatic has a broad selection of electric high force linear actuators – both roller and ball screw. We use standard roller screws to provide machine designers the longest possible service life, and we manufacture our own to ensure the highest quality.
Learn more
Download our guide, Which screw? Picking the right technology, for an overview of the advantages and disadvantages of each screw type.
You can go deeper with our review of screw selection for high force linear actuators.