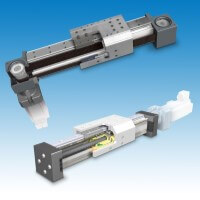
Timing belt or power screw drive: What’s best for a rodless actuator?
As a designer, you may be faced with an application in which you have to carry and support a load as well as move it. These are ideal applications for rodless electromechanical actuators.
While determining which rodless actuator model will suit your needs, you'll also need to select the type of drive: belt or screw. This blog will briefly explain these drive systems and summarize their advantages and disadvantages
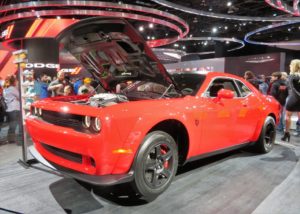
High-force linear actuator makes muscle car simulation possible
Tolomatic linear actuators are used worldwide in a myriad of industries for automation tasks like conveying, sorting, filling and more. Beyond conventional industrial applications they are also used in demanding, non-industrial applications. Some of these, such as simulators for flight, driving, testing and entertainment, require high-frequency moves to create a realistic experience. Here’s one such story, in which our electric high-force linear actuators helped simulate the experience of popping a wheelie in a true muscle car.
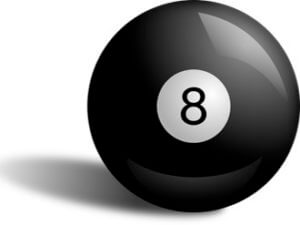
Electric linear motion vs. pneumatic. 8 things every designer should know about selection
There’s a debate in the machine design community about what’s the best linear motion technology—electric or pneumatic. There are proponents on both sides. As a manufacturer of both electric and pneumatic linear actuators, we’d like to bring some balance to the discussion.
Electric linear motion has benefits as do pneumatic solutions. This blog will give you eight factors to consider when you’re making this important selection
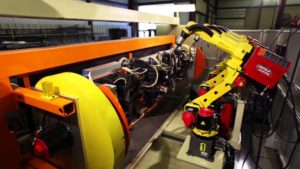
High-force linear actuators. Roller screws vs. ball screws
Not too long ago the only solution for high-thrust linear motion was fluid-powered cylinders that used high-pressure air or hydraulic oil. Although these cylinders could provide the force required, they could not deliver on requirements for infinite positioning, speed control, and low maintenance.
Now there are electric rod actuators that deliver high forces and excel at the other criteria as well. Often these electric high-force linear actuators utilize ball or roller screws. However, it’s a challenge to choose the right screw technology for a high-force application.
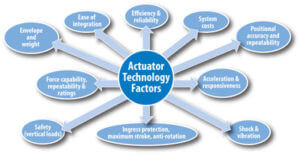
What’s best? Integrated linear actuators or traditional.
When you’re faced with designing a new piece of automation equipment, you have a lot on your mind. Concerns like performance requirements. How to design flexibility into the machine. How to keep costs down. How to pack the performance needed into a compact package.
You can rely to electric linear actuators to address these issues. They have inherent flexibility and long-term cost-efficiency. Once you choose electric linear motion, you can select either an integrated linear actuator or a traditional design. Both options have pluses and minuses that we’ll review here.

Innovate with linear motion: Online resource for integrating electric actuators into machine designs
For every application a machine designer tackles, they have to consider a unique set of requirements. Evaluating a variety of linear motion attributes is key to determining the optimal solution.
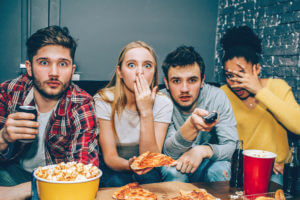
Stop Motion or High Definition?
It was a rough week for the whole team working on a new customer’s new machine design. Finally, it’s Friday night and you sit down on the couch to relax with your friends. You made some popcorn and just popped in a DVD recommended by your parents. They told you it’s a classic and might be a bit slow but it has a good story. The movie starts and after 30 seconds, your friends are giving you confused looks. The movie is very difficult to watch because it is filmed in stop motion. The images on the screen are frozen and jump from one to the next. Sometimes it is half a second between shifts and sometimes it can be several seconds. You can see the evening disintegrating and quickly move to switch out the movie to ‘The Fast and the Furious’ for some non-stop action.
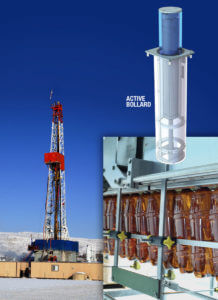
Avoid the pitfalls, gain all the benefits of replacing hydraulics with electric actuators
Electric actuators continue to find new and exciting places within automation processes from the mundane to some of the most extreme operating environments on the planet. Everyday machine designers seek alternative electric solutions to hydraulic cylinders for the very first time. However, there are many common pitfalls to properly sizing an electric equivalent. When sized correctly, replacement with high-force electric linear actuators can provide tremendous benefit in processes, quality and reducing your total cost of ownership.
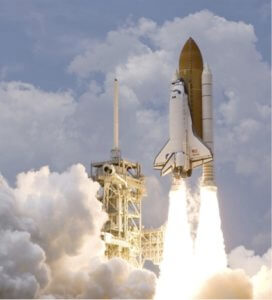
Failure not an option? How to avoid premature linear screw actuator failure
Some components are more mission-critical than others. A main worry of machine design engineers is making equipment that will last and avoiding need for field service calls to diagnose issues and replace failing components. At their core, electric linear screw actuators deploy mechanical technology such as ball bearings, ball screws and roller screws that have a finite life. These components do not last forever, even though that is the expectation of some customers. When asked “How long will this actuator last?” we provide our customers with a way to calculate, estimate and size the electric linear screw actuator to achieve the desired life for their applications.
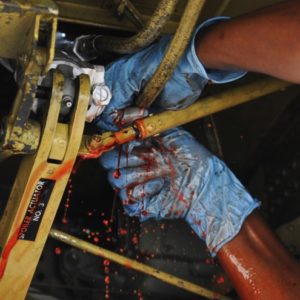
Overcoming hydraulic headaches by converting to electric linear motion solutions
Just 20 years ago, users of hydraulic systems struggled to find alternative technologies that could achieve the high force capabilities of hydraulic cylinders. Since then, motion control and automation technologies have rapidly evolved and electric linear actuator technology has emerged with capability to achieve the high forces (up to 100,000 lbf/445 kN) that were once the sole dominion of hydraulics. Even with these advancements, many manufacturers are either unaware -- or still in the process of discovering -- that viable electric options exist to address many of the challenges they face with hydraulic systems in high force applications.