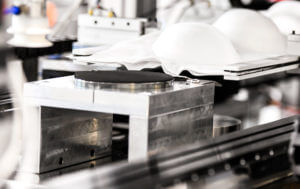
Fast and flexible: How to design a mask-making machine
Manufacturer rapidly invents a new way to make face masks in response to the COVID-19 pandemic. Electric actuators assist with linear motion technology.
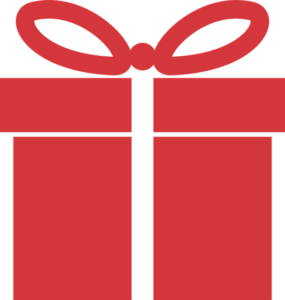
The best things come in sturdy packages
Automatic packaging machines must efficiently and consistently form and assemble boxes of all shapes and sizes. Pneumatic cylinders have been a long-standing and economcial solution for box-forming machines. However, electric linear actuators provide controlled movement and reliability advantages while meeting the same motion and force requirements.
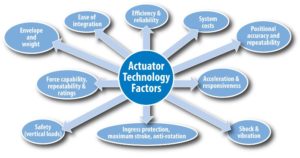
Traditional or integrated actuator? 10 factors to consider
Two common styles of electric rod actuators offer performance advantages depending on application and requirements. Knowing how to assess the differences and what to compare helps you meet your spec requirement.
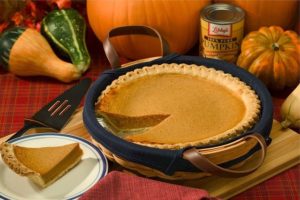
Easy as pie
Five best practices for designing and installing electric actuators in food processing equipment help create open/clean-in-place designs.
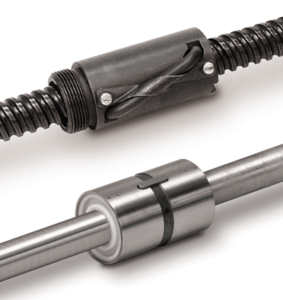
Actuator know-how for machine design engineers, Part 2
Machine designers face a variety of options when selecting linear actuators. It all comes down the best fit for the application: what solution provides the best results at a cost– effective price.
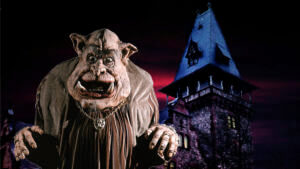
Haunted house animatronics: Expect the unexpected…(cue the evil laugh)
What makes scary creatures scary? It’s not smoke and mirrors. It’s motion control.
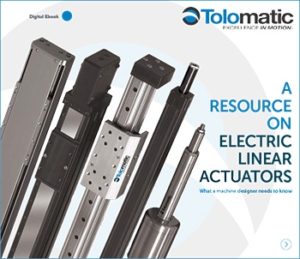
Specifying actuators 101: Actuator know-how for machine design engineers, Part 1
Learn key tips to simply actuator selection, starting with the initial decision of whether to specify an electric rod actuator or a rodless electromechanical actuator. It's all covered in our eBook, a ready-reference for your next maachine design project.
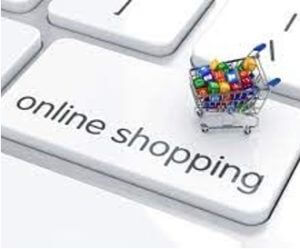
Motion control keeps material handling systems moving
In these stay-at-home days, online shoppers increase the need for accurate, fast and efficient material handling systems, from processing paper products to packaging, conveying and shipping. Electric actuation is bringing many benefits to applications that have typically been pneumatic.
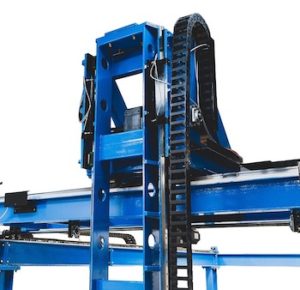
Linear actuators for gantry and multi-axis systems
Gantry and multi-axis systems are used throughout manufacturing to lift, position and move loads. Actuators and components are used to build two-dimensional designs with a simple XY axis, or three-dimensional designs with XYZ axis.
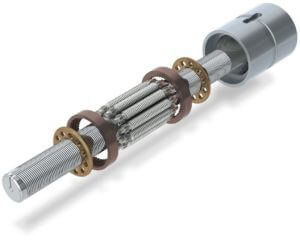
Roller screw technology for electric actuators
The unique design of a roller screw actuator offers longer life and higher thrust in a smaller package compared to ball screw actuators, increasing a machine designer’s ability to create compact machine concepts.