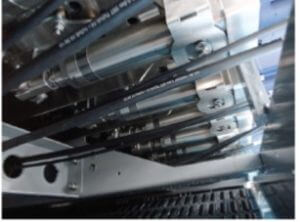
Electric actuator life in units of time: ball & roller screw actuators
A machine’s useful life depends on the life of its critical components. And machine designers frequently hear the question, “How long can I expect this machine to keep working?”
When electric linear actuators are used, calculating life can be straight-forward for ball screw and roller screw actuators. Since these screw types incorporate rolling elements as essential parts, you can use the L10 life formula for ball bearings.
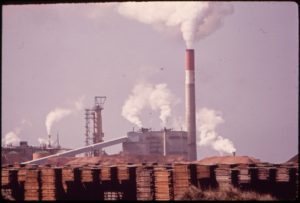
Solid-bearing, belt-driven linear actuator handles harsh environment
Many applications call for the carrying action of a rodless electromechanical actuator. And many of these need the high speed and long stroke capabilities of a belt-driven linear actuator. But what do you do when your application is in a dusty, harsh environment? Many rodless electromechanical actuators can’t handle these conditions. Their roller bearings get clogged with dust and stop working. Could a solid bearing be the solution?
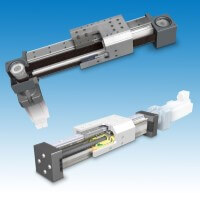
Selecting a rodless electromechanical actuator: belt- vs. screw-driven
Let’s say you’ve decided you need a rodless electromechanical actuator to carry a load in your application. Now you have to select a linear drive system. The two most common choices are screw drives and belt drives. Both drive types offer long life, low maintenance, and efficiency in converting the motor’s rotary motion to the carrier’s linear motion. However, each drive type is more suited to particular applications than others, depending on a few key factors.
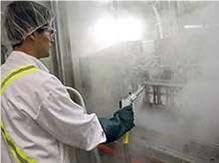
Electric linear actuator is clean-in-place, washdown ready
Stringent regulations govern the food processing industry. Food processing equipment and components, like electric linear actuators, must meet food safety regulations and stand up to clean-in-place (CIP) procedures. Food industry cleaning procedures may include regular washdowns with hot water, steam, high pressures, and caustic chemicals. Corrosion resistant materials and a water-shedding design are musts.
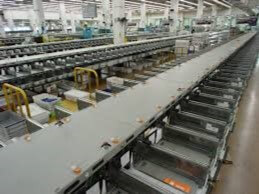
Linear actuator helps convert conveyor to electric
Every factory relies on some kind of conveyor system to take components, work pieces, or finished goods from one place to another. In fact, most factories have several conveying systems, each tailored to a specific need. Conveying equipment is varied and essential. Components in these systems, like linear actuators, must be able to meet these varied needs and provide reliable performance.
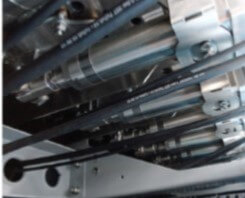
“How long will this actuator last?”
“How long will it last?” Every machine design engineer gets asked this question and will have to calculate the anticipated life of the machine – life that’s based on machine components including linear actuators. Engineers also have to consider expected life when they’re evaluating competing components.
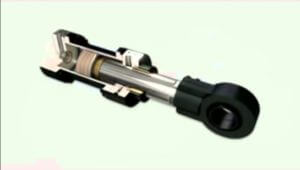
Hydraulic linear actuator advantages and disadvantages
Hydraulic cylinders are popular automation components in many industries. Like other types of linear actuator (pneumatic and electric), they are used to move loads in a straight line. A hydraulic actuator uses the energy in a pressurized liquid, usually oil, to achieve this linear motion, as opposed to compressed air (pneumatics) or electricity.
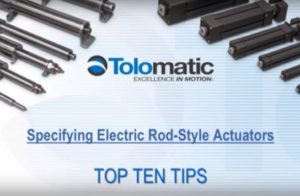
Webinar: tips on electric rod actuator selection
When you’re called on to specify electric linear actuators, one of the critical decisions you’ll face is whether to use a rodless or rod-style model. Either actuator type has advantages and disadvantages.
In general, if the actuator has to carry a load, a rodless product is what you need. However, if a load needs to be pushed or pulled, select a rod-style actuator.
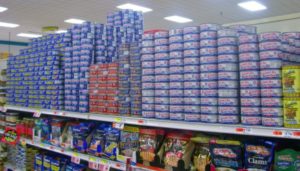
Hygienic linear actuator keeps it clean
The world of food production and packaging is broad, varied and ever-changing. That world needs filling machines as diverse as the range of food products they process. Some filling machines have to handle powders and dry solids while others must handle thin or thick liquids. Some machines fill to a specified level, and some fill by volume or weight. This wide variety of equipment has a unifying need, though -- a need for hygienic design that can keep food products uncontaminated and withstand even the most stringent cleaning procedures.
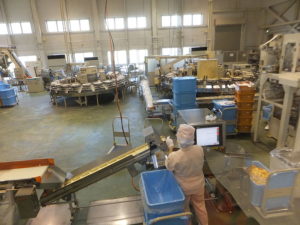
Linear actuators help prevent food contamination
Until recently, the food processing industry has handled contamination reactively. If a foodborne illness was traced back to contamination at a manufacturing plant, the FDA (Food and Drug Administration) had the manufacturer fix the problem.
The flaw in this system, though, was that most of these illnesses were preventable. The Centers for Disease Control and Prevention estimates that 48 million people (1 in 6 Americans) get sick, 128,000 are hospitalized, and 3,000 die each year from foodborne diseases. That makes food contamination a major public health issue.
The federal government stepped in to change the way the FDA and food producers operate with the Food Safety Modernization Act (FSMA) – signed into law in January 2011. This important legislation shifts the focus to preventing contamination problems instead of just responding to them. FSMA affects all automation components used in the industry, including linear actuators.