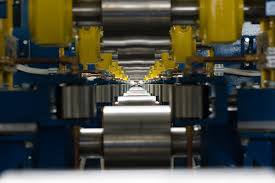
How to specify an electric linear actuator that’s industrial strength
Manufacturing environments can be challenging. There may be dust or metal shavings. There may be oil, coolant, or water. There may be corrosive agents like solvents, cleaners, and various chemicals and compounds.
All these factors impact the performance and life of components like electric linear actuators. Dust may clog the action or cause parts to wear out prematurely. Moisture may short electrical connections and cause rusting. Corrosive agents can eat away at housings, seals, fasteners, and more. Industrial environments call for industrial strength components.
A machine designer needs confirmation that a component will stand up to environmental factors.
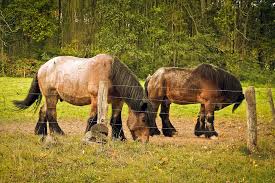
Electric rod actuator cleans up after hydraulics
Hydraulic cylinders are well-known linear motion workhorses in industrial machinery. They’re reliable, familiar, capable of high force, and affordable, but they’re not without disadvantages. The leading ones are fluid leaks, large footprint (with hydraulic power unit or HPU), cumbersome changeovers due to lack of programmability, and high maintenance costs.
The introduction of electric high force linear actuators means machine designers now have a choice. An electric rod actuator can replace a hydraulic cylinder and eliminate the need to clean up leaks.
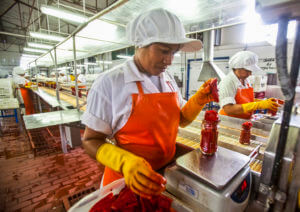
Machine design, FSMA, and electric rod actuators
Machine designers who serve the food processing industry face a huge opportunity. Purchases of equipment are expected to grow 7% a year to around $70 billion by 2020.
Not surprisingly, consumer demand is fueling this growth, but equally important in the U.S. is the Food Safety Modernization Act or FSMA. This legislation requires that food processors be proactive on food safety, that is, they must identify potential hazards and mitigate them.
A major result of the FSMA has been stepped up cleaning requirements and increased demand for hygienic equipment. That equipment needs washdown-ready components like electric rod actuators.
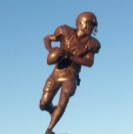
Go long! Selecting a long stroke electric linear actuator
Some linear actuator application requirements mean you have to go long. Long stroke, that is. Length of stroke is a critical factor in electric linear actuator selection. While some applications require moves of just inches or a few feet, others require moves of 10 feet or more. For an application requiring this kind of long stroke linear actuator, a belt driven rodless electromechanical actuator will be your solution.
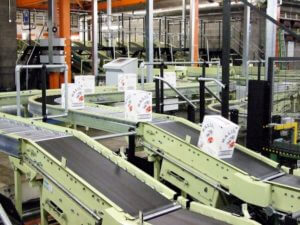
Integrated servo motor/controller/drive saves cost and plant space
Space is at a premium in most manufacturing operations. And of course, saving money is a constant goal. Plant managers are looking for ways to save money and space, so machine designers are tasked with creating ever more compact, affordable systems.
A new class of products addresses the needs for lower cost and efficient use of space: the integrated servo motor/controller/drive. These systems combine a servo motor and controller with a servo drive. They’re compact and eliminate the need for a drive cabinet.
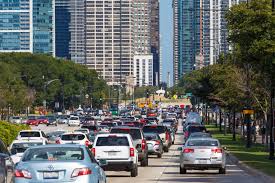
Lightweight servo actuators lower robotic RSW costs
Buyers want sturdy, well-built cars, so the quality of welds that hold auto bodies together is crucial to vehicle manufacturers. Manufacturers want strong welds that are consistently and accurately placed so the finished car looks both durable and attractive.
Welding robots for resistance spot welding (RSW) have been a boon to auto manufacturers because they provide consistent weld placement. But all welding robots need actuators to carry and power the weld gun. Those actuators have a huge impact on the consistent quality of welds. They can also impact the cost of robotic resistance spot welding.
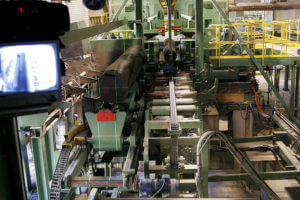
Roller screws for high force linear actuators. What type’s best?
Selecting the best screw type for a high force linear actuator can seem a daunting task, but it doesn’t have to be. Start with our Guide on the three common screw types for electric actuators, their advantages and disadvantages.
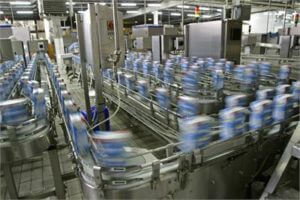
Electric linear actuator speeds up changeovers, lowers TCO
Time is money, as the saying goes, and it’s especially true in manufacturing. Reduce the time a process takes and you save operating costs. The concept of total cost of ownership (TCO) considers issues beyond a component’s purchase price like the downtime and labor costs associated with changing production set-ups.
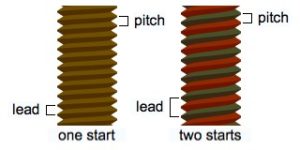
Acme, ball and roller screws for electric linear actuators
When you’re specifying a screw-driven electric linear actuator, you’ll need to consider the type of screw that best meets the needs of your specific application. Some manufacturers give you a choice so you can tailor the device precisely, and that’s a good thing since applications differ widely.
The basic types you’ll have to choose from are roller screws, ball screws and acme screws. There’s quite a lot a machine designer needs to know about these electric actuator screw types and how to select the right one. We offer a guide that helps your decision-making.
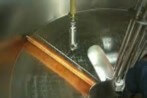
Machine design, clean in place (CIP) and linear actuators
Keeping clean is important, right? Well, in food and beverage processing and pharmaceuticals manufacturing keeping equipment clean is essential. Cross-contamination among batches causes problems, and food or beverage residue can grow harmful microorganisms. Many plants have clean in place (CIP) systems that deliver cleaning tailored to the needs of the facility including cleaning action (force, turbulence, direction), timing/duration (when, how often, how long), temperature, and type/strength of cleaning agent.
When you design equipment for these industries you need to keep cleanability in mind. Even components like electric linear actuators must stand up to cleaning procedures.