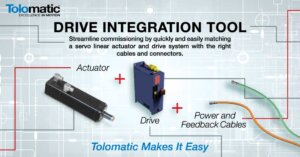
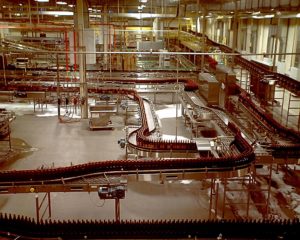
Integrated servo motor simplifies sourcing electric linear motion
An OEM’s component sourcing strategy will impact the final cost of a piece of automation equipment. While it can seem best to source parts from multiple suppliers, the time and cost involved in sourcing and integrating parts can raise the total machine cost significantly. Using a single-source approach and integrated components, like an integrated servo motor and controller for an electric linear motion system, can save time and money in the long run.
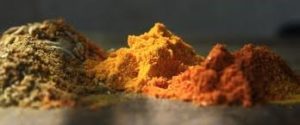
Integrated servo motor and controller ensures actuator precision, versatility
Powder-filling applications require precision and versatility. Precision to fill containers to the exact weight or volume. Versatility to accommodate changes.
Machine designers depend on electric linear actuators to deliver precision and versatility. And they’re finding that an integrated servo motor and controller coupled with a reliable electric actuator can do just that.
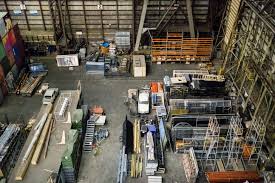
Why single-source your electric linear motion systems
The trend in industrial component sourcing is to eliminate waste, reduce costs and improve efficiency. This often means consolidating suppliers into single-source relationships. Single sourcing can build stronger relationships with suppliers, boost system performance and increase the speed of procurement.
Machine designers can use a single-source approach to reduce time spent on sourcing, installing and testing electric linear motion systems.
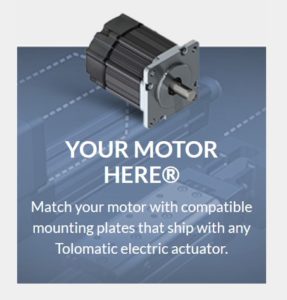
The easy way to get a complete electric linear motion solution
When your machine design calls for electric linear motion, you have lots of decisions to make. Like what actuator to use…and what motor. Select the right actuator and it will reward you with top performance, reliability and long service life. But an electric actuator that’s not up to the task can be a long-term problem. Then there’s motor selection and mounting. It can be a tough and touchy process. Even if you integrate the actuator and motor yourself, our Your Motor Here® program (YMH) will take the guesswork out of selecting and integrating the motor when you use one of our actuators.
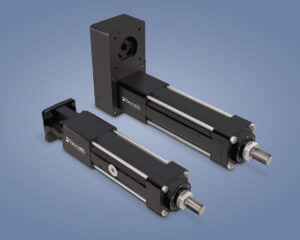
Motor mounting for electric linear motion
The motor is the power behind an electric linear motion system. An essential component. Designers can choose from a variety of motor types – stepper, servo, induction – and a myriad of motor manufacturers. Different applications will have different motor requirements. For those who elect to handle their own motor mounting, we’ve developed a new Technical Note on the subject.
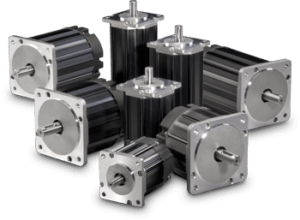
Motor selection for electric linear motion. Stepper vs servo
An electric linear motion system needs a motor. Unlike pneumatic cylinders that are powered by a central air compressor, electric linear actuators are powered by electric motors. The mechanisms in the actuator convert the motor’s rotary motion into linear motion. Machine designers can choose either servo or stepper motors for their electric linear actuator applications.
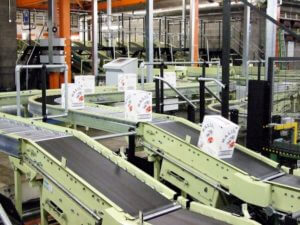
Integrated servo motor/controller/drive saves cost and plant space
Space is at a premium in most manufacturing operations. And of course, saving money is a constant goal. Plant managers are looking for ways to save money and space, so machine designers are tasked with creating ever more compact, affordable systems.
A new class of products addresses the needs for lower cost and efficient use of space: the integrated servo motor/controller/drive. These systems combine a servo motor and controller with a servo drive. They’re compact and eliminate the need for a drive cabinet.
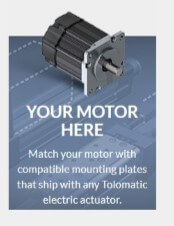
Electric linear actuators and motors. Getting the right fit.
An electric linear actuator can outperform a pneumatic model with superior control of speed, position, and force as well as provide better accuracy and repeatability. But that superior performance comes with complexity. Pneumatic cylinders commonly are simple, easy-to-understand components, while electric linear actuators are systems comprised of a motor, controller, cables, and actuator. Plus attaching a motor to an actuator usually requires some kind of adaptor or housing.
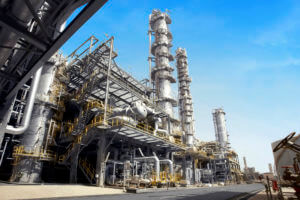
Brushless servo motors – more control for valves with linear actuators
Process industry engineers are looking to more sophisticated motion control solutions for valve automation because of an ever-growing need to improve productivity, increase efficiency, and minimize downtime.
These engineers must control the valves that regulate the flow of materials throughout a facility, and there are two basic ways to control these valves: linear motion (rising stem) and rotary motion (half turn or quarter turn). Powered rising stem valves are often used in mission-critical areas of a process. In these applications, reliability, repeatability, accuracy, and responsiveness are crucially important. These factors impact the type of valve actuation specified. There are traditional methods: pneumatic or hydraulic actuated systems and electric linear actuators driven by brush servo motors. Then there’s an emerging technology: brushless servo motor driven electric valve actuators.
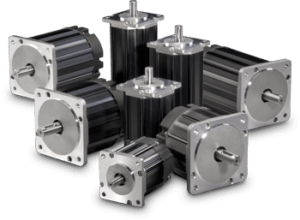
Stepper or servomotor? Selecting the best for your electric linear actuator.
When you specify an electric linear actuator for your application, you also need to specify a motor. The two basic types commonly used with linear actuators are stepper motors and servo motors. But what’s the difference? How do you choose? Here’s an explanation of the advantages and disadvantages of each motor type.