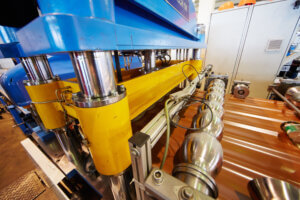
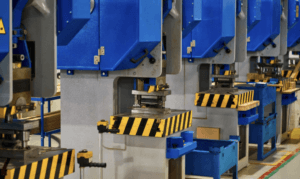
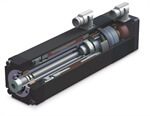
Small yet beefy
An internal servo motor makes for a smart, heavy duty and compact electric actuator package, one that is easy to retrofit or install new.
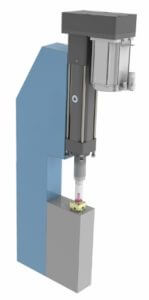
A pressing need
An electric servo-mechanical press offers all the versatility of a hydraulic press, with production speeds close to a flywheel press.
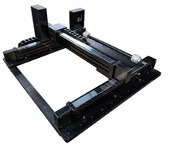
Gantry and multi-axis system: Build it your way
Gantries can be complicated and specialized. There are infinite variations for moving an object on multiple axes. But multi-axis motion control systems don’t have to be intimidating if you follow a straight-forward method that involves four steps.
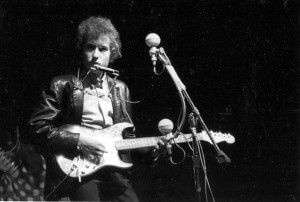
Go electric!
So maybe you missed Bob Dylan’s infamous switch to electric at the Newport Folk Festival in 1965. These days, you, too, can go electric—with an electromechanical system instead of hydraulic. Our new e-book helps you overcome pre-conceived notions and provides tips for a successful performance.
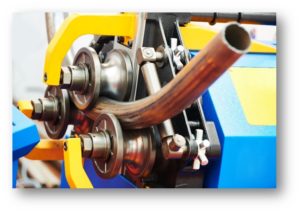
Making the case: Why convert a tube-bending machine from hydraulic to electric
Tube-bending machines have been driven by hydraulics for the past 80 years. Operators know how to get the best out of their machines, so why switch to electric cylinders? Yes, there are some disadvantages to going electric, but the fundamental reason to consider making the switch is simple: Electric cylinders make better parts. And that saves money. We'll discuss reasons to consider making the switch and take a look at two examples using electric-weld tubing and fluid-transfer tubing.
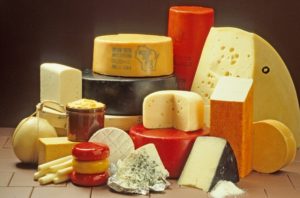
Cheese-making: Automating an ancient art for safety and efficiency
Electric linear motion enhances cheese processing and production.
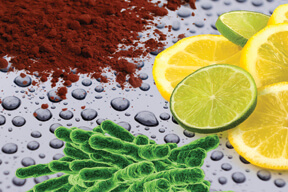
Linear motion for meat processing
Linear actuators used in meat processing are designed for corrosion resistance, washdown protection and bacterial growth prevention.
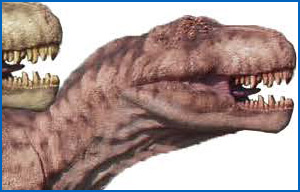
The Big Era of electromechanical linear actuators
Traditionally, hydraulic power is the go-to answer for heavy lifting. Now, high-force electric actuators have overtaken hydraulics in terms of flexibility, precision and reliability.
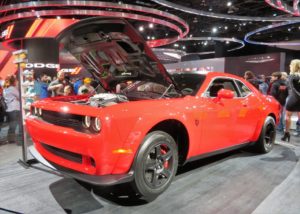
High-force linear actuator makes muscle car simulation possible
Tolomatic linear actuators are used worldwide in a myriad of industries for automation tasks like conveying, sorting, filling and more. Beyond conventional industrial applications they are also used in demanding, non-industrial applications. Some of these, such as simulators for flight, driving, testing and entertainment, require high-frequency moves to create a realistic experience. Here’s one such story, in which our electric high-force linear actuators helped simulate the experience of popping a wheelie in a true muscle car.
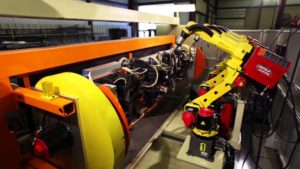
High-force linear actuators. Roller screws vs. ball screws
Not too long ago the only solution for high-thrust linear motion was fluid-powered cylinders that used high-pressure air or hydraulic oil. Although these cylinders could provide the force required, they could not deliver on requirements for infinite positioning, speed control, and low maintenance.
Now there are electric rod actuators that deliver high forces and excel at the other criteria as well. Often these electric high-force linear actuators utilize ball or roller screws. However, it’s a challenge to choose the right screw technology for a high-force application.
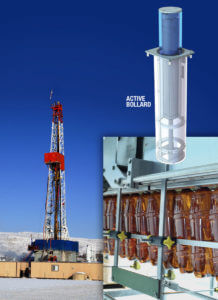
Avoid the pitfalls, gain all the benefits of replacing hydraulics with electric actuators
Electric actuators continue to find new and exciting places within automation processes from the mundane to some of the most extreme operating environments on the planet. Everyday machine designers seek alternative electric solutions to hydraulic cylinders for the very first time. However, there are many common pitfalls to properly sizing an electric equivalent. When sized correctly, replacement with high-force electric linear actuators can provide tremendous benefit in processes, quality and reducing your total cost of ownership.
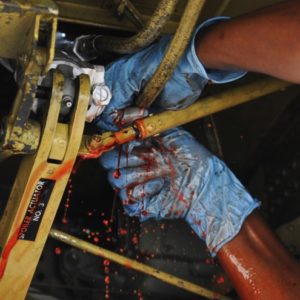
Overcoming hydraulic headaches by converting to electric linear motion solutions
Just 20 years ago, users of hydraulic systems struggled to find alternative technologies that could achieve the high force capabilities of hydraulic cylinders. Since then, motion control and automation technologies have rapidly evolved and electric linear actuator technology has emerged with capability to achieve the high forces (up to 100,000 lbf/445 kN) that were once the sole dominion of hydraulics. Even with these advancements, many manufacturers are either unaware -- or still in the process of discovering -- that viable electric options exist to address many of the challenges they face with hydraulic systems in high force applications.
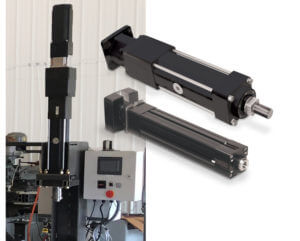
Electric high-force linear actuators improve powertrain assembly process and part quality
In automotive and heavy equipment industries machine designers and engineers know part quality and reliability are critical. That is why they often evaluate multiple linear motion technologies (hydraulics, pneumatic, electric) to determine the optimal solution for their component assembly or joining processes. It is imperative for their machines to produce quality parts that stand up to even the most demanding environments in harsh powertrain applications. Luckily, electric linear actuators offer engineers a solution for improving machine flexibility, precision, and reliability where legacy fluid power technologies (pneumatic and hydraulics) often fall short.
For an overview of how electric high-force linear actuators compare to hydraulic cylinders, see our white paper, Electric rod actuators versus hydraulic cylinders: a comparison of the pros and cons of each technology.
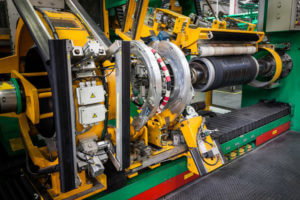
Converting From Hydraulic to Electric High-Force Linear Actuators with Force Feedback
Got a high-force linear motion application? If you do, chances are the first product solution to come to mind is hydraulic cylinders. After all, they’re relatively inexpensive (if you already have a hydraulic power unit – HPU – in place), compact (if the HPU’s somewhere else) and power-dense.
But what about the disadvantages of hydraulic cylinders? Leaks, operation and maintenance costs, and more? Now that there are electric high-force linear actuators, machine designers have a choice. It’s possible to convert an application from hydraulic to electric linear motion easily. Our guide, How to convert hydraulic cylinders to an electric actuator alternative, gives you a step-by-step explanation of the process.
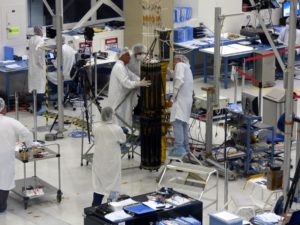
Electric high-force linear actuators keep medical manufacturing clean
Machine designers know that hydraulic cylinders offer compact size and excellent power density. Designers also know there are serious drawbacks that make these cylinders problematic in many applications – problems such as inevitable leaks. Those leaks can be a significant hazard in manufacturing environments that demand cleanliness such as medical equipment production. It used to be that hydraulic cylinders were the only choice when a designer needed a high-force linear actuator. Now there are electric high-force linear actuators that can replace hydraulics in many applications, offering clean operation as well as better accuracy and control.
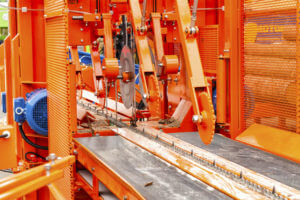
How to convert high-force linear actuators from hydraulic to electric
Things are changing in industrial automation. Many linear motion applications are getting more sophisticated with increased demand for control of process variables like velocity, thrust, acceleration/ deceleration and more.
It’s common for new applications that require high thrust from a linear actuator to use electric motion systems. Moreover, machine designers are converting existing hydraulic motion systems to electric.
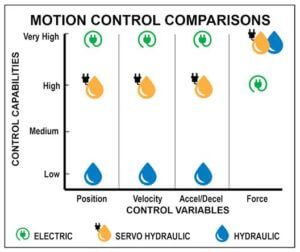
High force linear actuators: how to convert from hydraulic to electric
Electric linear actuators have come a long way – especially in the area of high force. Once upon a time when an application required high force, the usual linear motion solution was a hydraulic cylinder. However, as industrial automation gets more sophisticated and the need for precise control of speed, force and other variables grows, more engineers are considering electric high force linear actuators.
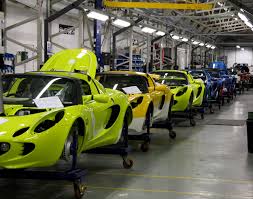
Changeover is faster with electric high-force linear actuators.
There’s no denying that hydraulic cylinders can provide reliable linear motion in the right applications. However, hydraulics cylinders often leak, and can be difficult to control. When a changeover is needed, adjusting a hydraulic cylinder is a time-consuming, hit-and-miss process. New electric high-force linear actuators are an alternative to hydraulics in many applications.

Electric extreme-force linear actuators beat hydraulics in metal casting
Metal casting is precise work conducted in a high-temperature environment. The process requires precise control of timing, flow rates and temperatures to yield good parts.
Unmolding a workpiece requires both force and control. It’s a task often left to hydraulic cylinders, but their high-force capabilities come with significant drawbacks, like inadequate control and messy leaks. New, electric extreme-force linear actuators offer precision and clean operation.
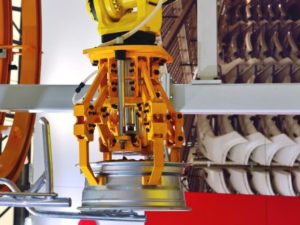
Lots more high-force linear actuator solutions with electric
Some machine designers still believe only hydraulic cylinders can handle high-force applications. But the fact is, electric high-force linear actuators are capable of 30,000 lbf (133 kN) maximum force and more, and they offer great affordability.
Some designers think the selection of electric high-force linear actuators is limited. But the truth is the range of electric high force actuation solutions is always expanding. With this expanding range of solutions, more existing applications can be converted to electric and new applications can gain the benefits of electric actuation.
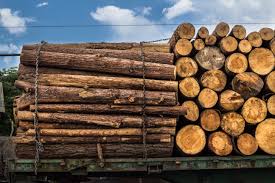
Extreme force electric linear actuator controls lumber drying
The lumber processing industry demands rugged, strong, reliable and accurate equipment in all its operations. Machine designers who serve this industry need extreme force linear actuators to move heavy loads. Hydraulic cylinders have been the go-to, but they have limitations, such as poor control, leaks, temperature sensitivity, maintenance requirements and lack of feedback. Now there are electric rod actuators powered by roller screws that can meet the requirements of these high force applications.
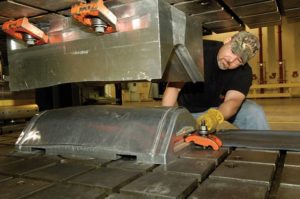
High force linear actuators: How to convert from hydraulics to electric
For high force linear actuator applications, machine designers often first look to hydraulic cylinders. For good reason, too – hydraulic cylinders can be a bargain to purchase, delivering high force at a low cost per unit of force. Plus, they’re rugged and well understood. But there’s another technology to consider. Electric linear actuators are available with high force capacities. These actuators are more flexible, precise and reliable than their hydraulic counterparts.
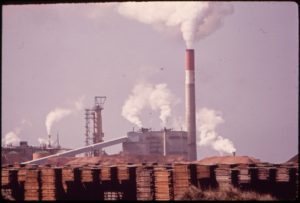
Electric high force linear actuator is tough enough to process lumber
The lumber industry has relied on the toughness and high force capabilities of hydraulic cylinders for years. But lately that reliance has been shaken. Hydraulic cylinders leak and can contaminate the fragile eco-systems in which lumber processing operates. Plus, hydraulic systems are only 40-55% efficient and cylinders require frequent maintenance. When combined, these factors can make hydraulic cylinders an expensive choice in the long run.
The introduction of electric high force linear actuators has given the lumber industry a new option for linear motion.
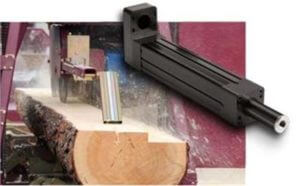
High force linear actuators – hydraulic vs electric [WEBINAR]
When your application calls for a high force linear actuator, you may believe that your only choice is a hydraulic cylinder. Hydraulics have long been the leading choice for automation equipment needing high force. However, now there are electric high force linear actuators that offer important advantages over hydraulics in terms of performance and total cost of ownership. Watch this webinar, and you may want to reconsider the merits of using an electric rod actuator.
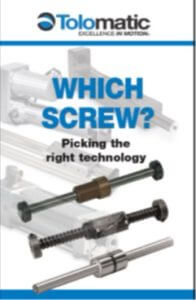
Which is best for high force linear actuators: Ball or roller screws?
If you’re selecting an electric high force linear actuator, you may believe you know the answer to the question in the headline. The force transmission prowess of roller screws is well known. But before you go to the expense of a roller screw linear actuator, take a careful look at the application. You may find that a ball screw actuator will do the job. And that could mean significant savings.
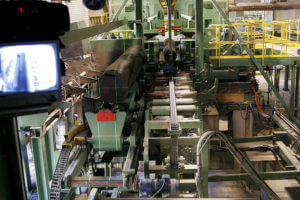
Roller screws for high force linear actuators. What type’s best?
Selecting the best screw type for a high force linear actuator can seem a daunting task, but it doesn’t have to be. Start with our Guide on the three common screw types for electric actuators, their advantages and disadvantages.
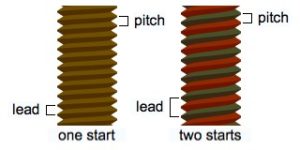
Acme, ball and roller screws for electric linear actuators
When you’re specifying a screw-driven electric linear actuator, you’ll need to consider the type of screw that best meets the needs of your specific application. Some manufacturers give you a choice so you can tailor the device precisely, and that’s a good thing since applications differ widely.
The basic types you’ll have to choose from are roller screws, ball screws and acme screws. There’s quite a lot a machine designer needs to know about these electric actuator screw types and how to select the right one. We offer a guide that helps your decision-making.
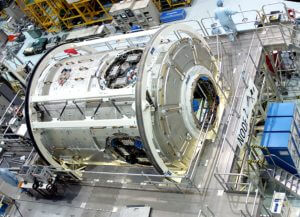
Corrosion resistant integrated linear servo actuator is high force
The electric rod actuator is an industrial workhorse, one you’ll find in a wide range of machine tool, conveying and positioning applications. A familiar mechanism, yes. But identifying one that’s compact, corrosion resistant and can deliver high force is a tall order. A corrosion resistant integrated linear servo actuator can be the answer.
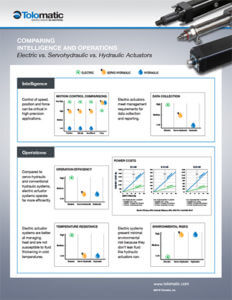
Hydraulic vs high force electric linear actuators: new infographic
Choosing the best linear actuator for a task takes a thorough understanding of the application. The basics like the weight of the load, the distance the load’s to be moved, and the speed and force needed are all important factors. A machine designer may also need to consider variables like environmental conditions, data collection and reporting, as well as flexibility/programmability requirements.
If the application calls for a high force linear actuator, the usual solution has been a hydraulic cylinder. However, high force electric linear actuators are now available (many with roller screws) and offer distinct advantages. Our new infographic compares the performance of electric, hydraulic and servohydraulic actuators on intelligence and operational parameters.
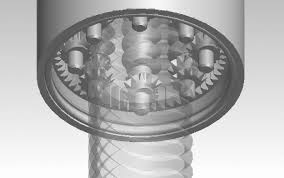
Electric high force linear actuators with roller screws rival hydraulic
When you’re specifying a high force linear actuator, your application’s requirements call the shots. It used to be that hydraulic cylinders were your only recourse when high force was needed. Now there are electric linear actuators with roller screws that rival the high force, high thrust, high torque capabilities of hydraulics. Plus, these electric actuators deliver high speed, great accuracy and repeatability and long life. Electric roller screw actuators are definitely an alternative to consider.
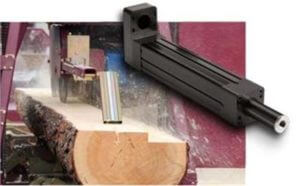
High force linear actuator: electric replaces hydraulic
It used to be that when a machine designer was confronted with a high force linear actuator application, the only solution was a hydraulic cylinder. That meant the designer had to factor in the bulky hydraulic power unit (HPU), the inevitable leaks of hydraulic fluid and the downtime produced by frequent maintenance.
Now there’s another option when a high force linear actuator is needed. There are electric linear actuator products that can meet demanding specifications with ease.
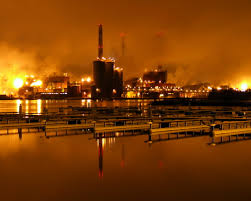
High force linear actuators: hydraulic vs roller screw actuators
Hydraulic cylinders have long been a leading choice for factory automation equipment needing a high force linear actuator. However, there have been advances in electric actuation (for example, the availability of roller screw actuators) which make these electric actuators suitable now for many high force applications.
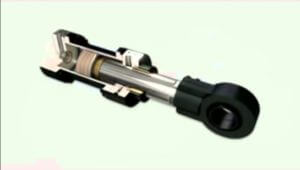
Hydraulic linear actuator advantages and disadvantages
Hydraulic cylinders are popular automation components in many industries. Like other types of linear actuator (pneumatic and electric), they are used to move loads in a straight line. A hydraulic actuator uses the energy in a pressurized liquid, usually oil, to achieve this linear motion, as opposed to compressed air (pneumatics) or electricity.
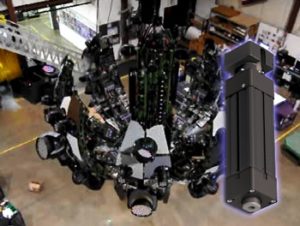
Something completely different – unique electric linear actuator applications
We all recognize that linear actuators are critical and much-used components in industrial automation systems. They’re at the heart of many machine tools, conveying configurations, and packaging systems. But what if we look beyond those industrial uses? Here are a few unique applications our actuators have found themselves in.